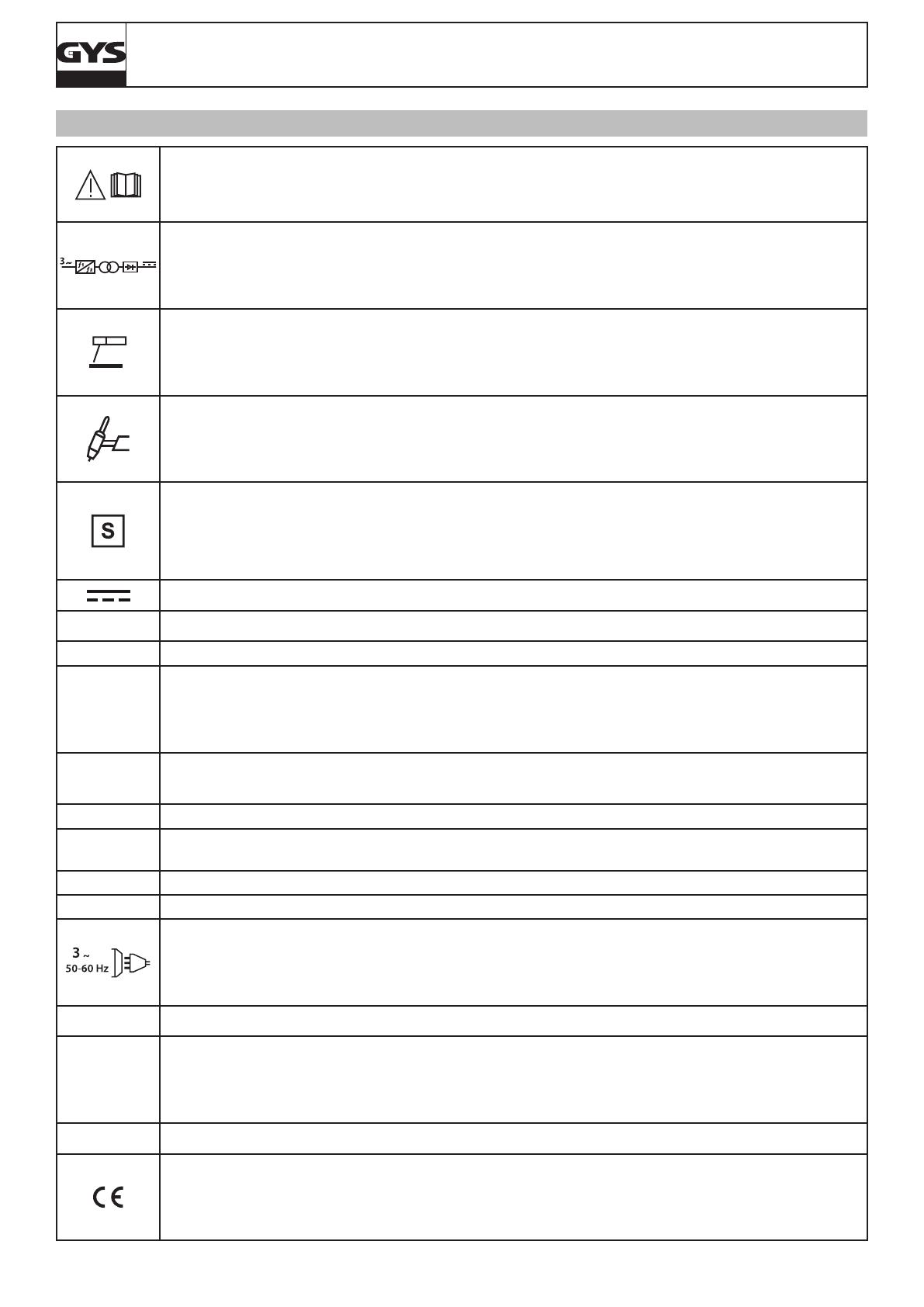
118
TITAN 400 DC
ICÔNES / SYMBOLS / ZEICHENERKLÄRUNG / ZEICHEN / СИМВОЛЫ / PICTOGRAMMEN
- Attention ! Lire le manuel d’instruction avant utilisation.
- Warning ! Read the instructions manual before use.
- Внимание! Прочтите инструкцию перед использованием
- ¡Cuidado! Lea el manual de instrucciones antes de su uso.
- Let op! Lees voor gebruik aandachtig de gebruiksaanwijzing door.
- Attenzione! Leggere il manuale d’istruzioni prima dell’uso.
- Source de courant de technologie onduleur délivrant un courant continu.
- Inverter technology welding current source delivering direct current.
- Fuente de corriente de tecnología inverter de corriente continua.
- Invertergleichstromquelle (DC)
- Источник тока с технологией преобразователя, выдающий постоянный ток.
- Stroomvoorziening met UPS technologie, levert een continue stroom.
- Generatore di corrente con tecnologia inverter che rilascia una corrente continua.
- Soudage à l’électrode enrobée - MMA (Manual Metal Arc)
- MMA welding (Manual Metal Arc)
- Schweißen mit umhüllter Elektrode (E-Handschweißen)
- Soldadura con electrodo revestido - (MMA - Manual Metal Arc)
- Сварка электродом с обмазкой (MMA – Manual Metal Arc)
- Lassen met beklede elektrode - MMA (Manual Metal Arc)
- Saldatura ad elettrodo rivestito - MMA (Manual Metal Arc)
- Soudage TIG (Tungsten Inert Gaz)
- TIG welding (Tungsten Inert Gaz)
- TIG- (WIG-)Schweißen (Tungsten (Wolfram) Inert Gas)
- Soldadura TIG (Tungsten Inert Gaz)
- Сварка TIG (Tungsten Inert Gaz)
- TIG lassen (Tungsten Inert Gaz)
- Saldatura TIG (Tungsten Inert Gaz)
- Convient au soudage dans un environnement avec risque accru de choc électrique. La source de courant elle-même ne doit toutefois pas être placée dans de tels
locaux.
- Suitable for welding in an environment with an increased risk of electric shock. However, the machine itself should not be placed in such an environment.
- Geeignet für Schweißarbeiten im Bereich mit erhöhten elektrischen Risiken. Trotzdem sollte die Schweißquelle nicht unbedingt in solchen Bereichen betrieben werden.
- Adaptado para soldadura en lugar con riesgo de choque eléctrico. Sin embargo, la fuente eléctrica no debe estar presente en dichos lugares.
- Подходит для сварки в среде с повышенным риском удара током. В этом случае источник тока не должен находиться в том же самом помещении.
- Geschikt voor het lassen in een ruimte met verhoogd risico op elektrische schokken. De voedingsbron zelf mag echter niet in een dergelijke ruimte worden geplaatst.
- Adatto per saldatura in un ambiente con alto rischio di scosse elettriche. La fonte di corrente non deve essere comunque localizzata in tali locali.
- Courant de soudage continu - Direct welding current - Gleichschweißstrom - - Corriente de soldadura continua - Постоянный сварочный ток. - DC lasstroom - Cor-
rente di saldatura continua..
U0
- Tension assignée à vide - Off load voltage - Tensión asignada en vacío - Leerlaufspannung - Номинальное напряжение холостого хода - Nullastspanning - Tensione
assegnata a vuoto
Up
Tension de crête assignée - Allocated peak voltage - Tensión de pico asignada - Nominale piekspanning - Tensione di picco assegnata
X(40°C)
- Facteur de marche selon la norme EN60974-1 (10 minutes – 40°C).
- Duty cycle according to standard EN 60974-1 (10 minutes – 40°C).
- Einschaltdauer: 10 min - 40°C, richlinienkonform EN60974-1
- Ciclo de trabajo según la norma EN60974-1 (10 minutos – 40°C).
- ПВ% согласно норме EN 60974-1 (10 минут – 40°C).
- Inschakelduur volgens de norm EN60974-1 (10 minuten – 40°C).
- Ciclo di lavoro conforme alla norma EN60974-1 (10 minuti – 40°C).
I2
I2: courant de soudage conventionnel correspondant / I2: Corresponding conventional welding current / I2: entsprechender Schweißstrom / I2: corriente de soldadura
convencional correspondiente / I2: соответствующий номинальный сварочный ток. / I2: corresponderende conventionele lasstroom / I2: corrente di saldatura
convenzionale corrispondente
A
Ampères - Amperes - Ampere - Amperios - Амперы - Ampère - Amper
U2
- U2: Tensions conventionnelles en charges correspondantes / U2: Conventional voltage in corresponding loads. / U2: entsprechende Arbeitsspannung / U2: Tensiones
convencionales en cargas correspondientes. / U2: Номинальные напряжения при соответствующих нагрузках. / U2: Conventionele spanning bij overeenkomstige
belasting / U2: Tensioni convenzionali in cariche corrispondenti
V
Volt - Volt - Volt - Voltio - Вольт - Volt
Hz
Hertz - Hertz - Hertz - Hercios - Герц - Hertz
- Alimentation électrique triphasée 50 ou 60Hz.
- Three-phase power supply 50 or 60Hz
- Dreiphasige Netzversorgung mit 50 oder 60 Hz
- Alimentación eléctrica trifásica 50 o 60Hz
- Трехфазное электропитание 50 или 60Гц
- Driefasige elektrische voeding 50 of 60 Hz.
- Alimentazione elettrica trifase 50 o 60Hz.
U1
- Tension assignée d’alimentation - Rated power supply voltage - Netzspannung - Номинальное напряжение питания. - Nominale voedingsspanning - Tensione asse-
gnata d’alimentazione
I1max
- Courant d’alimentation assigné maximal (valeur efcace).
- Maximum rated power supply current (effective value).
- Maximaler Versorgungsstrom (Effektiwert)
- Corriente de alimentación eléctrica asignada máxima (valor ecaz).
- Максимальный сетевой ток (эффективное значение).
- Nominale maximale voedingsstroom (effectieve waarde).
- Corrente di alimentazione nominale massima (valore efcace).
I1eff
- Courant d’alimentation effectif maximal - Maximum effective rated power supply current - Maximaler tatsächlicher Versorgungsstrom - Corriente de alimentación efec-
tiva máxima - Максимальный эффективный сетевой ток. - Maximale effectieve voedingstroom - Corrente di alimentazione effettiva massima.
- Matériel conforme aux directives européennes. La déclaration UE de conformité est disponible sur notre site (voir à la page de couverture).
- Device complies with Europeans directives. The EU Declaration of Conformity is available on our website (see cover page).
- Die Geräte entsprechen die europäischen Richtlinien. Die Konformitätserklärung nden Sie auf unsere Webseite.
- Aparato conforme a las directivas europeas. La declaración de conformidad UE está disponible en nuestra página web (dirección en la portada).
- Apparaat in overeenstemming met de Europese richtlijnen. De E.U. verklaring van overeenstemming kunt u downloaden op onze website (adres vermeld op de oms-
lag).
- Dispositivo conforme alle direttive europee La dichiarazione UE di conformità è disponibile sul nostro sito internet (vedere alla pagina di copertina).