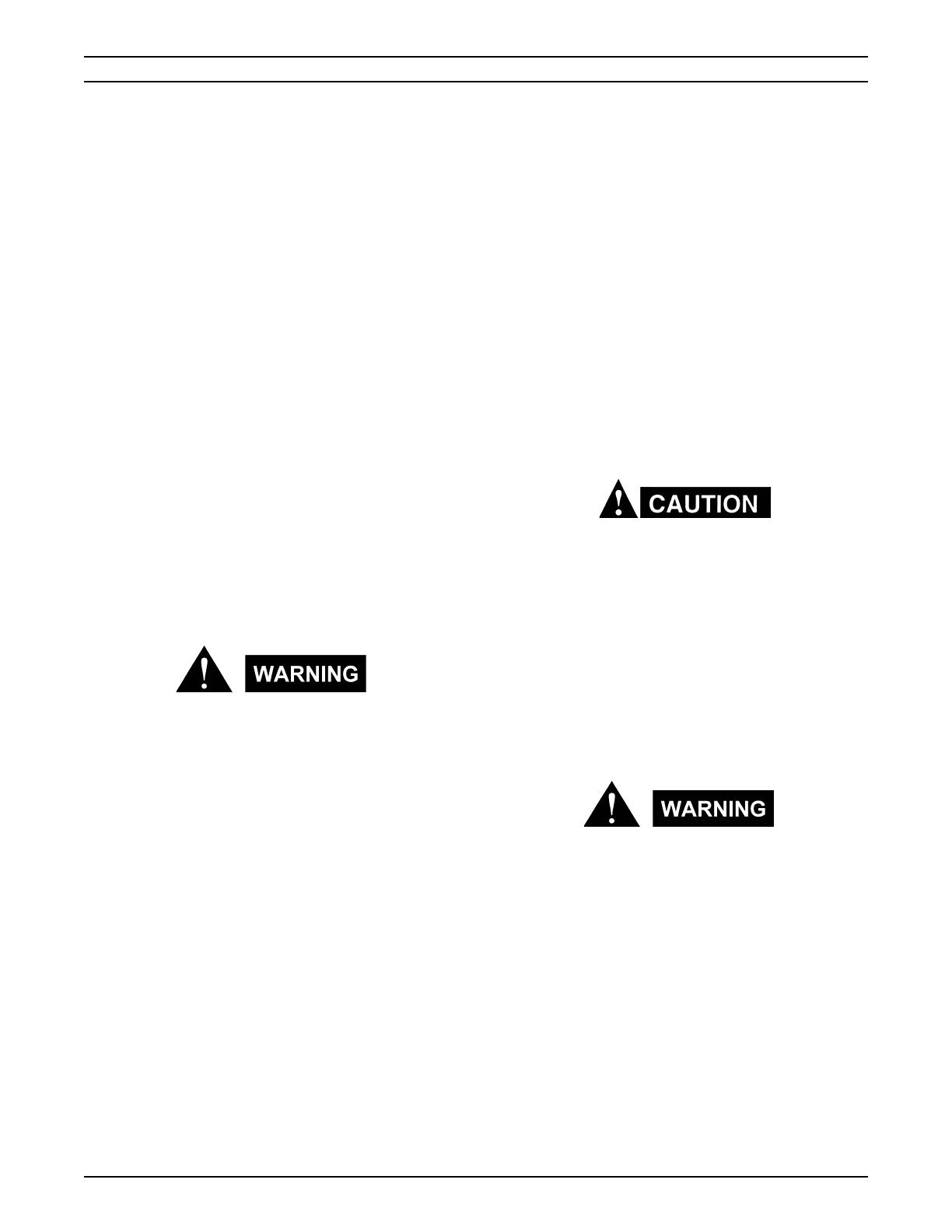
SECTION 6 MAINTENANCE
75
C. Water Cooling. Coolant enters the torch through the
power cable (-), circulates through the torch body and
the electrode, crosses over to the nozzle (+) section
of the torch body through nonconductive bypass
tubes, travels back through the body and circulates
between the nozzle retainer and the nozzle, then back
through the torch body to the junction box via the pilot
arc cable.
D. Plasma Cut and Start Gas. These gases enter the
torch through connections that house check valves
within the torch body. The valves acting in conjunc-
tion with solenoid valves control the back and forth
switching of start and cut gases. See Figure 6-2 for
further explanation of this system.
E. Shield Gas. Shield preflow, cut shield and postflow
enter the torch through one connection, pass through
the torch body, through the shield gas diffuser and
then out of the orifice in the shield cap that surrounds
the plasma jet.
F. Power and Pilot Arc Lines. Coolant IN to the torch
is through the power cable (-). Coolant OUT from the
torch is through the pilot arc (+) line.
6.6 TORCH MAINTENANCE
Make sure power switch on the console is in the OFF
position and primary input power is disconnected.
A. Always check the three O-rings on the torch body
before each day's operation and replace if any damage
or wear is noted. Apply a thin coat of silicone grease
to O-rings before assembling to torch. The O-ring P/
N 638797 inside the torch body that seals the nozzle
is especially critical. Because of its location, damage
or wear is not readily apparent. Replacing this ring on
a daily basis is recommended. Be careful not to
scratch or damage the inside surface of the torch. A
toothpick works well for removing the O-ring. The ring
can be replaced without removing the water baffle P/
N 21725, if however the baffle is to be removed,
always use a 3/16 inch (5 mm) hex wrench or nut
driver.
B. Water leaks, moisture, or coolant dripping from the
vent hole in the sleeve indicates service line damage.
If service lines have to be replaced always use two
wrenches to avoid twisting the metal tubes.
C. The torch sleeve P/N 21757 is threaded onto the torch
body. If the sleeve is too tight to be readily removed
by hand, use a large adjustable wrench on the flats
located on the body or lightly tighten these flats in a
vise. With the body secured in this manner, the use
of two hands on the sleeve may break the sleeve free,
if not, use a strap wrench. Always check service line
connections for leaks before replacing the sleeve.
D. Be especially careful not to get dirt or foreign matter
in the check valve fittings where the plasma cut and
start gases are attached. If however dirt or other
foreign matter gets into the check valves, they can be
dismantled, then cleaned and replaced.
The seat, ball and spring must not be damaged when
handling. Also, Do NOT substitute any other spring
or ball. If they are dropped, lost, or damaged they
must be replaced with genuine ESAB replacement
parts. Changes, substitutions or damaged parts will
affect set pressures and cause poor starting and
piercing.
6.7 PT-24 CONSUMABLE REMOVAL,
INSPECTION AND INSTALLATION
Make sure power switch on the console is in the OFF
position and primary input power is disconnected.
NOTE
When changing consumables, if the nozzle retainer/
diffuser seems especially stubborn and difficult to re-
move, the console is probably still on. With the console
on, the pump will be running and coolant pressure behind
the retainer will prevent it from turning freely. Check the
console before making further attempts to remove the
nut. Notice also that a small amount of coolant will be lost
each time consumables are removed. This is normal and
eventually the coolant will have to be replaced. Check the
coolant before each operation.