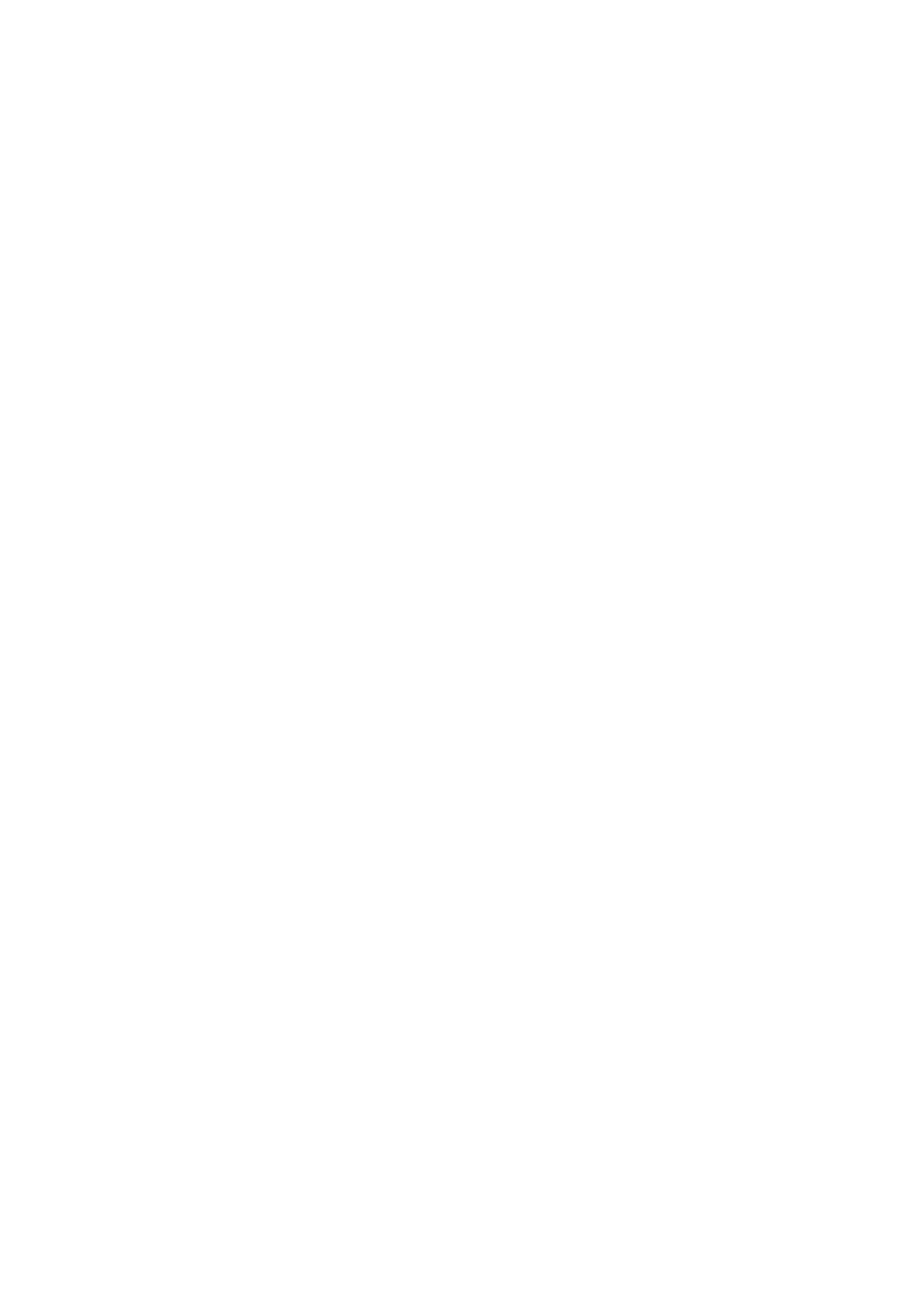
INSTALLATION
-- 1 9 --
dfa3i1ga
10. Kontaktausrüstung
S Einfachdraht 1,6 -- 2,5 mm (4,0 mm). Light duty (D20)
Ist Standard im A6 SFD1 (LD--Ausführung) und wird bei Bedarf verwendet,
z.B. auf engem Raum, Drahtdimensionen bis zu 4,0 mm.
Kontaktrohr D20 mit Kontaktdüse (M12--Gewinde), siehe Tabelle auf
Seite 54.
G Die Düse mit einem 10er Schlüssel festziehen, um einen guten Kontakt
zu erhalten.
Für dünne Drahtelektroden, Durchm. 1,6 -- 2,5 mm, Führungsrohr und sepa-
rates Dünndrahtrichtwerk verwenden.
G Die Klammer für das F ührungsrohr im M12--Loch für die feste Richtrolle
des Standard --Richtrollenwerks montieren. Das Führungsrohr soll bis zur
Kontaktdüse reichen und die Länge ist evtl. abzuschneiden, so daß der
Abstand zur Vorschubrolle ca. 5 mm beträgt.
G Das Dünndrahtrichtwerk an der Oberseite der Klammer für das Richtrol-
lenwerk montieren.
S Einfachdraht 3,0 -- 6,0 mm. Heavy duty (D35)
Als Standard im A6 SFD1 einbegriffen.
Kontaktrohr D35 mit Kontaktbacken verwenden. Siehe auch Anmerkung betr.
Kontaktrohr D20 für Drahtdimension bis zu 4,0 mm auf engem Raum.
G Standardrichtrollenwerk zur A6 benutzen, mit einem Drahtrichtwerk be-
stehend aus einer festen und einer ansetzbaren Richtrolle.
G Die Kontaktbacke mit mitgelieferten M5 --Schrauben montieren, ein Teil
der Kontaktbacke im festen Kontaktrohr und ein Teil in der losen Hälfte
des geteilten Kontaktrohrs.
G Die lose Hälfte mit dem Gleitkontakt mit der Inbusschraube M8 montie-
ren und fest anziehen, so daß zwischen Kontaktbacke und Drahtelektro-
de ein guter Kontakt erhalten wird.
S Fülldrähte.
Für Fülldrähte kann sowohl Kontaktrohr D20 als auch D35 verwendet
werden.
Wenn Kontaktbacke (D35) verwendet werden, sind diese mit mäßiger Kraft
festzuziehen, so daß die Fülldrähte nicht deformiert werden. Sicherstellen,
daß ein guter Kontakt zur Drahtelektrode erhalten wird.
S Doppeldrahtelektrode.
Immer Kontaktrohr D35 für Doppeldrahtelektrode mit Führungsrohr und se-
paratem Drahtrichtwerk verwenden.
G Klammer für das Führungsrohr im M12 --Loch der festen Drahtrichtrolle
des Standard --Drahtrrichtrollenwerkes montieren. Das Führungsrohr
(Heavy Twin) soll die Kontaktbacke oder den Adapter für die Kontaktdü-
se (Light Twin) berühren.
G Die Länge des Führungsrohres so anpassen, daß der Abstand zur Vor-
schubrolle ca. 5 mm beträgt.