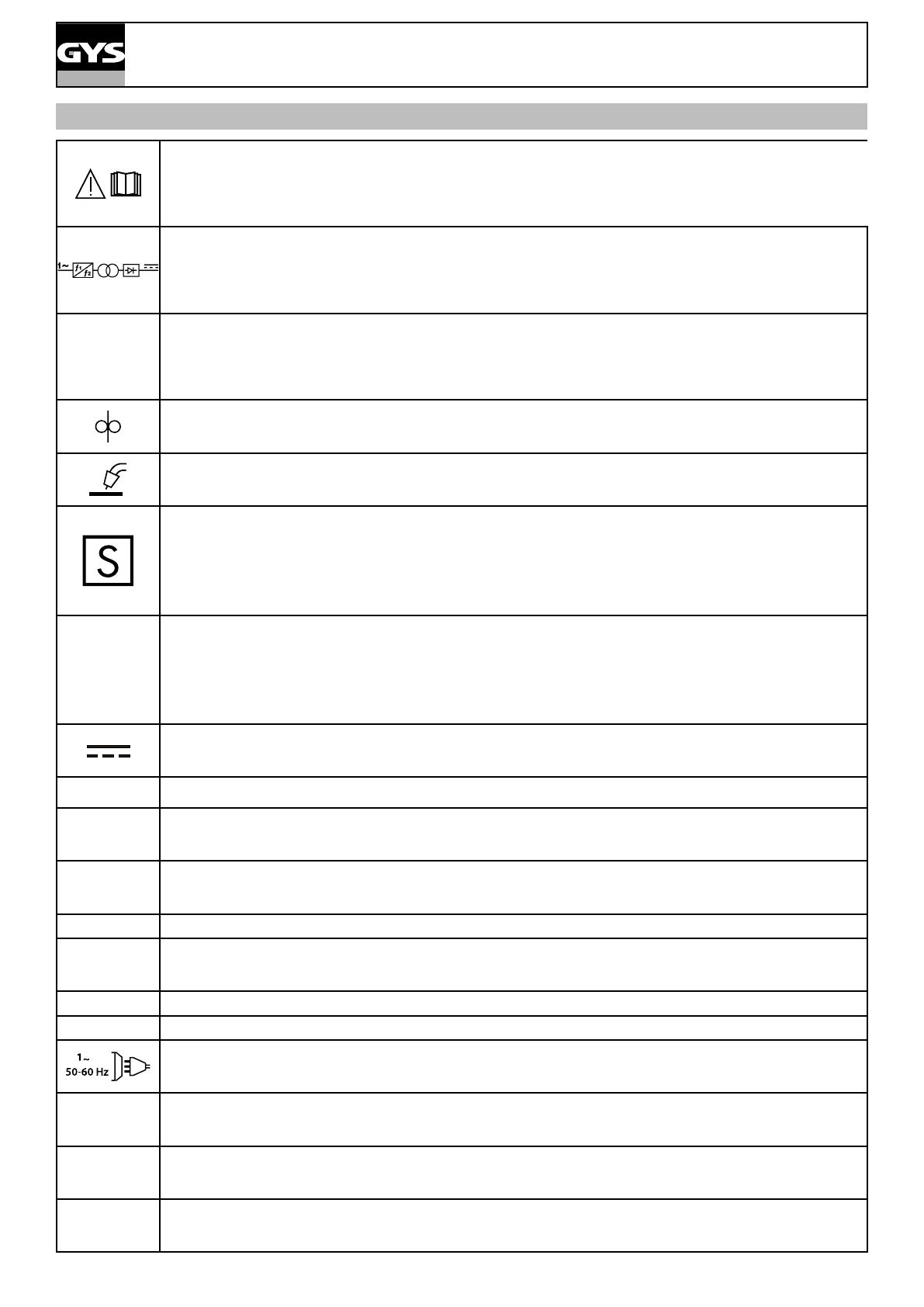
AUTOPULSE 220
117
ICÔNES / SYMBOLS / SYMBOLE / ICONOS / ZEICHENERKLÄRUNG / СИМВОЛЫ
- Attention ! Lire le manuel d’instruction avant utilisation.
- Caution ! Read the user manual.
- Achtung! Lesen Sie die Betriebsanleitung.
- Cuidado, leer las instrucciones de utilización.
- Внимание ! Читайте инструкцию по использованию.
- Let op! Lees voorzichtig de gebruiksaanwijzing.
- Attenzione! Leggere il manuale d’istruzioni prima dell’uso
- Source de courant de technologie onduleur délivrant un courant continu.
- Undulating current technology based source delivering direct curent.
- Invertergleichstromquelle.
- Fuente de corriente de tecnología ondulador que libera corriente continua.
- Источник тока с технологией преобразователя, выдающий постоянный ток.
- Stroombron met UPS technologie, levert gelijkstroom.
- Fonte di corrente con tecnologia inverter che rilascia una corrente continua.
EN60974-1
EN60974-5
EN60974-10
Class A
- La source de courant de soudage est conforme aux normes EN60974-1/-5/-10 et de classe A.
- This welding machine is compliant with standard EN60974-1/-5/-10 of class A.
- Die Stromquelle entspricht der Norm EN60974-1/-5/-10. Gerät Klasse A.
- El aparato es conforme a las normas EN60974-1/-5/-10 y de clase A.
- Источник сварочного тока отвечает нормам EN60974-1/-5/-10 и относится к классу A.
- De lasstroomvoorziening is conform aan de EN60974-1/-5/-10 en klasse A norm.
- La fonte di corrente di saldatura è conforme alle norme EN60974-1/-5/-10 e di classe A.
- Vitesse du l
- Wire speed
- Drahtgeschwindigkeit
- Velocidad de hilo
- Скорость проволоки
- Draadsnelheid
- Velocità di lo
- Soudage MIG / MAG
- MIG / MAG welding
- MIG / MAG-Schweißen
- Soldadura MIG / MAG
- Сварка MIG / MAG
- MIG / MAG lassen
- Saldatura MIG / MAG
- Convient au soudage dans un environnement avec risque accru de choc électrique. La source de courant elle-même ne doit toutefois pas être placée dans de tels
locaux.
- Suitable for welding in environment with an increased risk of electric shock. However this a machine should not placed in such an environment.
- Geeignet für Schweißarbeiten in Bereichen mit erhöhten elektrischen Risiken. Trotzdem sollte die Schweißquelle nicht unbedingt in solchen Bereichen betrieben
werden.
- Adaptado para soldadura en lugar con riesgo de choque eléctrico. Sin embargo, la fuente eléctrica no debe estar presente en dichos lugares.
- Подходит для сварки в среде с повышенным риском удара током. В этом случае источник тока не должен находиться в том же самом помещении.
- Geschikt voor het lassen in een ruimte met verhoogd risico op elektrische schokken. De voedingsbron zelf moet echter niet in dergelijke ruimte worden geplaatst.
- È consigliato per la saldatura in un ambiente con grandi rischi di scosse elettriche. La fonte di corrente non deve essere localizzata in tale posto.
IP21
- Protégé contre l’accès aux parties dangereuses des corps solides de diam>12,5mm (équivalent doigt de la main) et contre les chutes verticales de gouttes d’eau.
- Protected against rain and against ngers access to dangerous parts.
- Schutz vor Eindringen von festen Fremdkörpern (Durchmesser >12,5mm = Finger einer Hand). Schutz gegen Berühren mit einem Finger und senkrecht fallendes
Tropfwasser.
- Protegido contra el acceso a partes peligrosas con el dedo, y contra las caídas verticales de gotas de agua.
- Защищен против доступа твердых тел диаметром > 12,5 мм (размером с палец руки) в опасные места. Защищен против доступа пальцев в опасные места и -
против вертикального попадания капель воды.
- Beschermd tegen toegang tot gevaarlijke delen met een vinger en tegen verticaal vallende waterdruppels.
- Aree Pericolose protette per impedire il contatto con l’utente, e contro cadute verticali di gocce d’acqua.
- Courant de soudage continu.
- Direct welding current.
- Gleichschweißstrom
- Corriente de soldadura continua.
- Постоянный сварочный ток.
- DC lasstroom
- Corrente di saldatura continua.
U0
- Tension assignée à vide - Off load voltage - Leerlaufspannung - Tensión asignada en vacío - Номинальное напряжение холостого хода - Nullastspanning - Tensione
nominale a vuoto
X(40°C)
- Facteur de marche selon la norme EN60974-1 (10 minutes – 40°C).
- Duty cycle according to standard EN 60974-1 (10 minutes – 40°C).
- Einschaltdauer: 10 min - 40°C, richtlinienkonform EN60974-1
- Ciclo de trabajo según la norma EN60974-1 (10 minutos – 40°C).
- ПВ% согласно норме EN 60974-1 (10 минут – 40°C).
- Inschakelduur volgens de norm EN60974-1 (10 minuten – 40°C).
- Ciclo di lavoro conforme alla norma EN60974-1 (10 minuti – 40°C).
I2
I2: courant de soudage conventionnel correspondant.
I2: corresponding conventional welding current
I2: entsprechender Schweißstrom
I2: corriente de soldadura convencional correspondiente.
I2: соответствующий номинальный сварочный ток.
I2 : overeenkomstige conventionele lasstroom
I2: corrente di saldatura convenzionale corrispondente.
A
Ampères - Amperes - Ampere - Amperios - Амперы - Ampère - Amper
U2
- U2: Tensions conventionnelles en charges correspondantes.
- U2: Conventional voltage in corresponding loads.
- U2: entsprechende Arbeitsspannung
- U2: Tensiones convencionales en cargas correspondientes.
- U2: Номинальные напряжения при соответствующих нагрузках.
- U2 : Conventionele spanning in corresponderende belasting.
- U2: Tensioni convenzionali in cariche corrispondenti.
V
Volt - Volt - Volt - Voltio - Вольт - Volt
Hz
Hertz - Hertz - Hertz - Hercios - Герц - Hertz
- Alimentation électrique monophasée 50 ou 60Hz
- Single phase power supply 50 or 60Hz
- Einphasige Netzversorgung mit 50 oder 60Hz
- Alimentación eléctrica monofásica 50 o 60 Hz
- Однофазное напряжение 50 или 60Гц
- Enkel fase elektrische voeding 50Hz of 60Hz
- Alimentazione elettrica monofase 50 o 60Hz
U1
- Tension assignée d’alimentation.
- Rated power supply voltage.
- Netzspannung
- Tensión asignada de alimentación eléctrica.
- Номинальное напряжение питания.
- Nominale voedingsspanning.
- Tensione nominale di alimentazione.
I1max
- Courant d’alimentation assigné maximal (valeur efcace).
- Maximum rated power supply current (effective value).
- Maximaler Eingangsstrom (Effektiwert)
- Corriente de alimentación eléctrica asignada máxima (valor ecaz).
- Максимальный сетевой ток (эффективное значение).
- Aangewende maximale voedingsstroom (effectieve waarde).
- Corrente di alimentazione nominale massima (valore effettivo).
I1eff
- Courant d’alimentation effectif maximal.
- Maximum effective rated power supply current.
- Maximaler tatsächlicher Eingangsstrom.
- Corriente de alimentación eléctrica máxima.
- Максимальная эффективная подача тока.
- Maximale effectieve voedingsstroom
- Corrente di alimentazione effettiva massima.