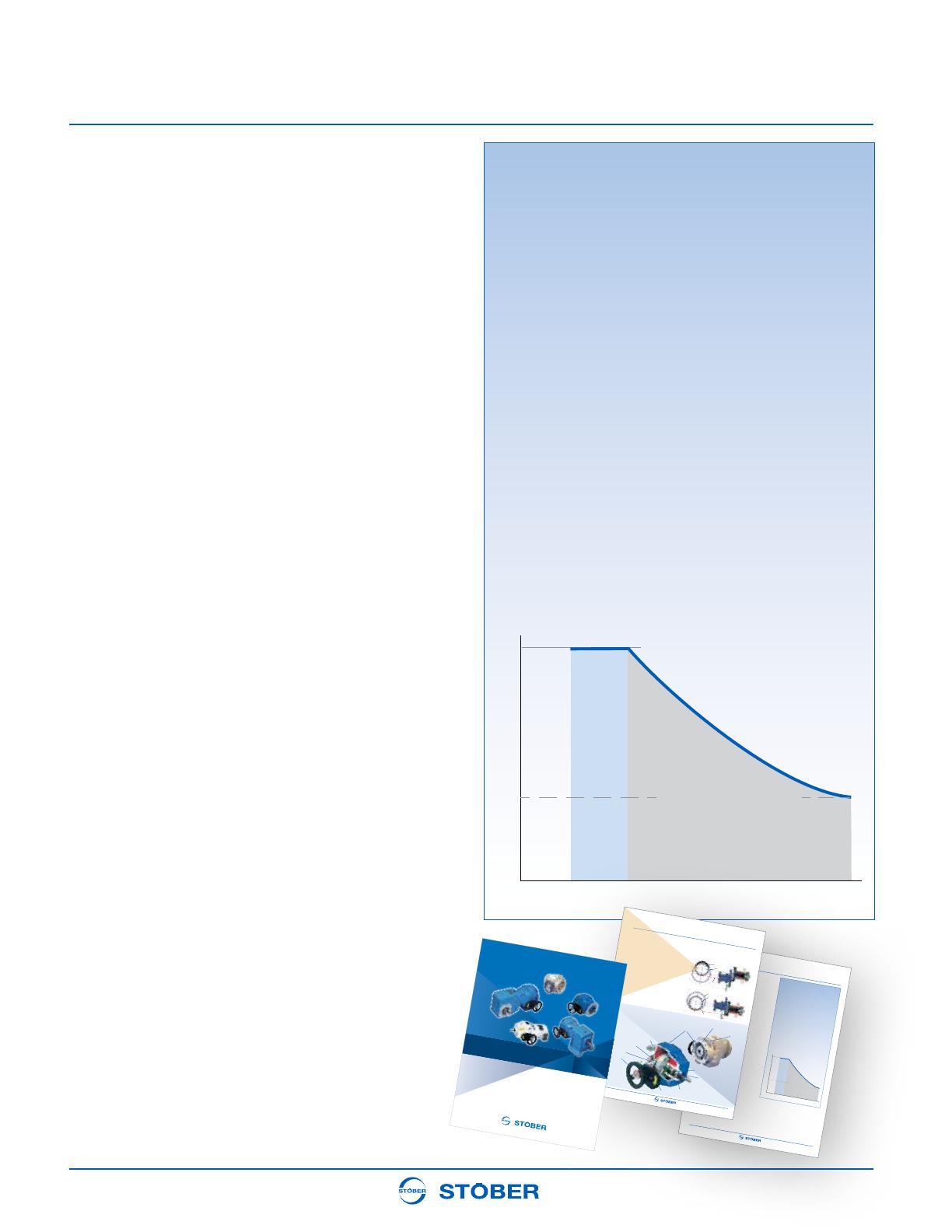
4ComTrac® Adjustable Speed Drives V.27 800.711.3588 • www.stober.com
ComTrac® Adjustable Speed Drives
ComTrac TD Performance
Complete ComTrac performance data is provided in the
ComTrac catalog available for download from our website.
Note that all performance rangs shown in this document and
in the ComTrac catalog selecon tables are based on standard
NEMA motors at 1750 RPM speed, 60 Hz operaon.
Several opons for ComTrac drives are included in the
ComTrac product catalog. In addion, the following opons
are also available:
• 50 Hz operaon for export
• Motor enclosures
For applicaon and selecon assistance for these opons and
others, contact your local STOBER distributor.
Non-Standard Application Conditions
For constant horsepower applicaons, or any of the
nonstandard applicaon condions shown below, contact
STOBER technical support.
Unusual Loading Condions:
• Heavy shock load
• High inera load
• Load reversals or overhauling loads
• More than ten starts per hour
Unusual Environmental Condions:
• High altudes – above 5000 feet
• Corrosive chemicals
• Excessively dusty or abrasive environments
• Ambient temperatures below 25° F or above 125° F
Nonstandard Motors:
• Motor frame sizes other than those shown in the tables
Nonstandard Mounng:
• Output sha up or down (V5 or V6 mounng)
Not Recommended for Mounng:
• Explosive environments of any type
Two Ranges of Performance
A ComTrac drive generally produces constant output
torque because of its mechanical operaon, whereas
an inducon motor produces constant horsepower and
constant speed. Combined, ComTrac with an inducon
motor provide opmum ulity and economy.
As shown in the chart below, a ComTrac drive has two
operang regions.
1. Constant torque between the drive’s absolute
minimum speed and transion speed.
2. Constant horsepower between the transion speed
and maximum speed.
Since ComTrac applicaons typically require constant torque
over the enre speed range, an adequate service factor to
protect the tracon ring from damage is applied. When
selecng a ComTrac drive, it is important to choose a
unit which will not allow the cone and ring system to
be over powered by the motor. As shown in the chart, a
drive should always be selected so that the output torque
required is well below the torque capability of the cone
and the ring system.
Transion
Minimum
Maximum
Rated Torque @ Max Speed
Max Torque Capacity of Cone/Ring
Torque — Output (in.lbs.)
Speed — Output
Constant
Torque
Operang
Range
Constant
HP
Operang
Range
Torque/Speed Performance (Overhung Load)
C
o
n
s
t
a
n
t
H
P
M
o
t
o
r
O
u
t
p
u
t
(
M
a
x
)
We highly recommend you download product literature from our
website pertaining to your installaon, and to keep it with this
manual and other records on your ComTrc and MGS products
10 800.711.3588 • www.stober.com
ComTrac
®
Adjustable Speed Drives V.27
ComTrac
®
Adjustable Speed Drives
Motor Performance
The rangs shown in the ComTrac selecon tables are based
on standard NEMA motors with the following specicaons:
• 1750 RPM speed
• 60 Hz operaon
Application Matched Options
Several opons for ComTrac drives are included in this
catalog. Addionally, the following opons are also available:
• 50 Hz operaon for export
• Motor enclosures
For applicaon and selecon assistance for these opons and
others, contact your local STOBER distributor.
Non-Standard Application Conditions
For constant horsepower applicaons, or any of the
nonstandard applicaon condions shown below, contact
STOBER technical support.
Unusual Loading Condions:
• Heavy shock load
• High inera load
• Load reversals or overhauling loads
• More than ten starts per hour
Unusual Environmental Condions:
• High altudes – above 5000 feet
• Corrosive chemicals
• Excessively dusty or abrasive environments
• Ambient temperatures below 25° F or above 125° F
Nonstandard Motors:
• Motor frame sizes other than those shown in the tables
Nonstandard Mounng:
• Output sha up or down (V5 or V6 mounng)
Not Recommended for Mounng:
• Explosive environments of any type
Two Ranges of Performance
A ComTrac drive generally produces constant output
torque because of its mechanical operaon, whereas
an inducon motor produces constant horsepower and
constant speed. Combined, ComTrac with an inducon
motor provide opmum ulity and economy.
As shown in the chart below, a ComTrac drive has two
operang regions.
1. Constant torque between the drive’s absolute
minimum speed and transion speed.
2. Constant horsepower between the transion speed
and maximum speed.
Since ComTrac applicaons typically require constant torque
over the enre speed range, an adequate service factor to
protect the tracon ring from damage is applied. When
selecng a ComTrac drive, it is important to choose a
unit which will not allow the cone and ring system to
be over powered by the motor. As shown in the chart, a
drive should always be selected so that the output torque
required is well below the torque capability of the cone
and the ring system.
Transion
Minimum
Maximum
Rated Torque @ Max Speed
Max Torque Capacity of Cone/Ring
Torque — Output (in.lbs.)
Speed — Output
Constant
Torque
Operang
Range
Constant
HP
Operang
Range
Torque/Speed Performance (Overhung Load)
C
o
n
s
t
a
n
t
H
P
M
o
t
o
r
O
u
t
p
u
t
(
M
a
x
)
7
ComTrac
®
Adjustable Speed Drives V.27
800.711.3588 • www.stober.com
Contact Point
Motor Slide Down
Motor Slide Up
Drive Cone
Tracon Ring
Drive Cone
Tracon Ring
ComTrac Overview
Here’s How Simple it Is!
Turn the handwheel and the pinion moves the rack on the
motor slide up or down to adjust the output speed as lile or
as much as you want.
ComTrac
®
Operation
The ComTrac® drive is an adjustable speed tracon drive. It
operates by transfering power between a motor mounted
drive cone and a tracon ring (see illustraon below). Forced
together, the drive cone and tracon ring transmit torque
through a spring-loaded torque compensator assembly.
(NOTE: While the drive is at rest, the spring inside the torque
compensator produces a slight contact pressure between the
drive cone and tracon ring. Unlike other mechanical drives,
this minimal spring pressure allows speed changes to be
made even while the drive is stopped.)
When the drive is started, the load compensang cams move
against each other to increase pressure between the drive
cone and tracon ring. During operaon, these cams maintain
the proper amount of pressure between the drive cone and
tracon ring in proporon to the output load torque required.
Movement of the motor and drive cone are accomplished
through the use of a handwheel aached to a rack and
pinion. By turning the handwheel, the motor is easily raised
or lowered on a dust resistant motor slide.
Speed changes are made by changing the relave running
diameters of the drive cone and the tracon ring (see
illustraon at right). Lowering the motor and drive cone
posions the contact point between the cone and tracon
ring in the slower running center of the drive cone which
decreases output speed. As the motor and drive cone are
moved upward, the contact point between the cone and ring
moves to the faster running outer diameter of the drive cone
and output speed increases.
Minimum Speed
Maximum Speed
Torque Compensator Assembly
Load Compensang Cams
NEMA C-face Input
Wrench Kit
Drive Cone
Handwheel
Speed
Adjustment
Speed Adjustment Dial
Cast Iron Housing
Access Cover with Wrench Kit
Collet Clamp Ring
Fricon (Tracon) Ring
Flange Assembly
Speed Control
Made Simple!
™
ComTrac
®
Adjustable Speed Drives